Application of Arc Sensing Technology in Weld Seam Tracking
2019-10-04 15:08:21
The essence of the weld tracking is to align the welding arc with the welding position to ensure the welding joint forming and welding quality. It detects the information of the arc from the weld through the sensor, and adjusts the relative position of the arc and the weld through the automatic control system to make the deviation Small until it disappears. Therefore, a simple, reliable and sensitive weld seam tracking sensor is essential for highly automated welding robots.
According to the characteristics of the sensor, the weld tracking sensor can be divided into the following types: arc sensor, electromagnetic induction sensor, photoelectric sensor and mechanical sensor, among which the arc sensor is used as a real-time sensing device and other types of sensors. Compared with the characteristics of simple structure, low cost and fast response, it is an important development direction of the weld tracking sensor.
1. Characteristics of the arc sensor
The arc sensor has its unique advantages: 1 the detection point is the welding point, there is no problem of the sensor first, and it is a completely real-time sensor. 2 Since the arc itself acts as a sensor, it is not affected by arc deflection caused by wire bending. 3 not only can track the sensing, ensure the stability of the welding parameters, but also improve the forming effect of the weld. 4 anti-light, electromagnetic, thermal interference, long service life.
2. The working principle of arc sensing
The arc sensor utilizes the change of the welding current or the arc voltage during the welding process to obtain whether the arc center deviates from the weld seam, and uses this as the sensing information, and the real-time performance is strong, and the tracking effect is good. In the V-shaped weld shown in Figure 1, the sensor measures the position of the weld gun at the weld by means of a oscillating arc, the principle being that the torch must be running at the center of the weld and maintaining a defined height for the root of the weld. If the route is deviated during the welding process due to the manufacturing error of the workpiece, the dry elongation of the wire on both sides of the weld is different, resulting in the actual welding current being different from the set current. The shorter the dry elongation, the larger the actual current; the longer the dry elongation, the smaller the actual current. Using this principle, the sensor's signal is fed back to the robot control system in real time, allowing the robot to react quickly and accurately. Real-time correction of the trajectory of the robot during the welding process can achieve accurate repositioning of the weld seam, that is, the originally programmed trajectory will be automatically corrected according to the actual weld trajectory, ensuring that the trajectory centerline is always at the center of the groove.
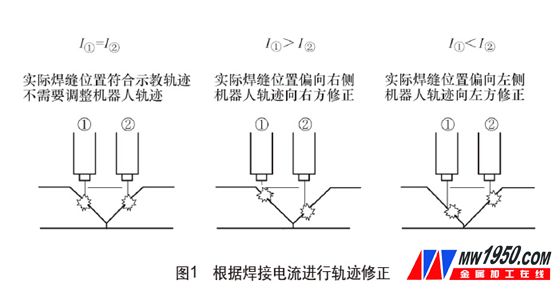
3. Application of arc sensing in igm welding robot
At present, arc sensors have been widely used in welding robot systems. The arc sensing technology can independently correct the welding path in real time to adapt to the change of weld position and make it in various forms of welds (V-shaped, Y-shaped, U-shaped, and angular). During the welding process of the weld), the welding torch is accurately guided along the weld trajectory for real-time monitoring and automatic correction.
The igm welding robot of Fig. 2, the weld seam tracking system is mainly composed of the arc sensing circuit board of Fig. 3 and the shunt resistor, and the electrical principle thereof is shown in Fig. 4. The arc sensing circuit board A130 is inserted into the PC of the KUKA control cabinet, and the shunt resistors R1 and R2 are respectively located on the side of the two welding power sources. During the welding process, the shunt resistor is detected in real time, and the signal is fed back to the arc sensing circuit board. The arc sensing circuit board calculates and judges the detected signal and sends it to the PC computer. The signal is processed by the PC computer. The command signal is transmitted to the internal axis drive of the robot, and the drive is controlled to make the robot arm make a compensation action, adjust the posture of the welding torch, and ensure that the center line of the welding track is at the center of the weld bevel.
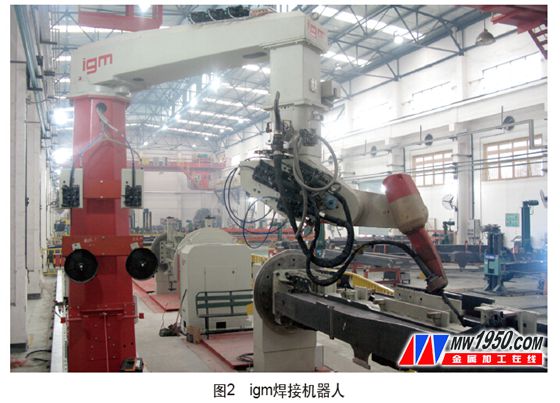
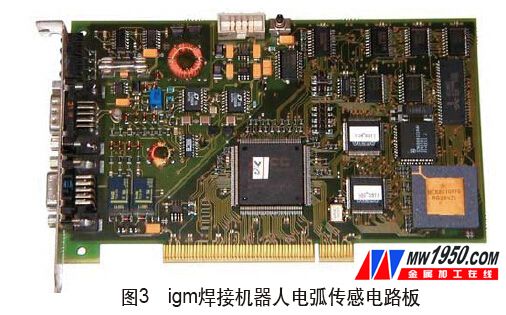
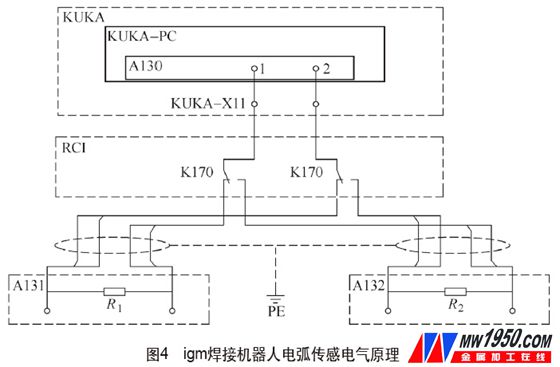
The arc sensing technology of the igm welding robot actually determines the center position of the weld according to the real-time detection feedback of the shunt resistance to the welding current change, and the welding gun makes corresponding adjustment actions to realize the automatic tracking of the actual weld trajectory.
4. The main influencing factors of arc sensing
The main factors affecting arc sensing are: sensing sensitivity (pendulum width / swing height), torch attitude (angle), swing frequency, welding speed, workpiece condition, grounding condition and welding power. Therefore, in order to obtain a good sensing effect, it is necessary to repeatedly adjust and test the welding power supply parameters for various types of welds, and finally determine the optimal welding parameters corresponding to different workpieces and different welds.
5 Conclusion
Research and development of automated and intelligent welding robot control system is an important means to ensure welding quality, improve production efficiency and improve labor intensity of workers. The characteristics of arc sensing technology are very beneficial to the realization of welding intelligent control, so arc sensing technology More important application value will be reflected in welding automation.
Vinyl Wall Covering,Arte Wallcovering,Dutch Wallcoverings,Classical Wallcovering
Shandong Fiberglass Group Corp. , https://www.en-glasstex.com