Cathodic electrophoretic coating process for new technology of automotive fastener surface treatment
The rapid development of China's machinery industry has put forward higher and higher requirements for the quality of vehicle products. The high safety, high environmental protection and diversified personality of the vehicle have also been reflected in the surface protection technology of fasteners. At present, the surface treatment technology of automotive fasteners mainly includes oxidation (blackening), phosphating, electroplating (zinc, zinc-nickel alloy, decorative chrome), Dacromet coating, and the like. It is well known that oxidation treatment has defects such as high energy consumption, unstable process, and weak film layer; the corrosion resistance of the phosphate film is poor; the passivation treatment liquid and the Dacromet coating of the plating contain Cr6+, which is not environmentally friendly. The corrosion resistance of ordinary plating layers can reach 500-1000h. However, the cost is high, the film layer has poor wettability (120h resistance to heat and humidity), and it is not wear-resistant.
In order to improve the quality of fastener surface treatment and meet the requirements of environmental protection regulations, in addition to the above surface treatment process, foreign countries such as the United States and Ford Motor Company use the cathodic electrophoretic coating process to surface treatment of bolts. According to different quality requirements of fasteners, different salt spray tests can be used for 240-1000h, and the friction coefficient of paint film is suitable, which does not affect product assembly. It can replace the passivation process of electroplating and is beneficial to environmental protection. .
Cathodic electrophoretic coating has a high degree of mechanization, environmental protection, and excellent corrosion resistance of paint film. It has been used in vehicle painting for many years. The application of fasteners in China is still a vacancy in China. It is indeed a new technology. A new area of ​​innovation in fastener products. According to the types and performance requirements of automotive fasteners, high-strength 8.8, 10.9 bolts for automotive chassis, engine and transmission were tested. The plan is as follows:
1 black cathode electrophoretic coating, electrophoretic coating for fastener coating;
2 black cathode electrophoretic coating, the formula is adjusted, suitable for fastener coating;
3 black cathode electrophoretic coating, electrophoretic coating for ordinary parts coating.
Focus on testing several key properties of the coated (plated) layer of fasteners. a. Corrosion resistance (salt spray test) performance. b. Resistance to hot and humid performance. c. Assembly performance.
At present, domestic high-strength fasteners for automobiles rely on imports. An important bottleneck for localization of fasteners is the control of friction coefficient. Under the conditions of ensuring the assembly performance, the salt spray resistance test and the hot flash resistance are as long as possible. In addition, the paint film does not fall off when assembled with an air wrench. These are the key technologies for the fastener coating process.
Using electrophoretic coatings 1, 2, and 3, there is no change in the surface of the 500h paint film, and the total friction coefficient and the dispersion coefficient (uniform value) of the friction coefficient are better than those of the electroplated zinc parts. The electrophoretic coating 1 has the best solution, the coating thickness is 15-18μm, the salt spray resistance test is 240-1000h, and the comprehensive cost is 15-20 yuan/mm2.
To this end, the application of the electrophoretic coating on automotive fasteners has led to the following conclusions.
1. The process scheme of fasteners using electrophoretic coating for surface treatment is feasible;
2, must use the special electrophoretic coating of fasteners, in order to achieve the surface quality requirements of fasteners;
3. Compared with the electro-galvanizing process, the various indexes of the electrophoretic coating process are improved, and the cost is low.
We can produce the A/SA106B/C steel pipes according to the ASME SA106 and ASTM A106 standards, and we have been sold about 250000 MT the oversea markets at recent 10 years. YC has been granted a number of approval certificate by international institutions, such as Nuclear pipe certificate, 914mm Cylinder certificate, API monogram and certificate, ISO9001 by TUV NORD, ISO14001/OHSAS18001 by CQC, approvals from Shipping Classification Bureaus like DNV, RINA, ABS, Lloyd, GL, Bureau Veritas, and permit of exporting to Europe as PED 2014/68/EU and AD 2000 certificates for pressure pipes, CPD (Construction Products Directive), etc.
Chengde have been working on the research.manufacture and sale of seamless pipe about 30 years, and the advantage of core competence is more prominent by integrate in technical.management and market with PCC.
1 The Piercing and rolling technology of Chengde possesses a number of patents in designing and manufacturing the equipment. The production is efficient and flexible, and the quality is stable.
2 The material grade is complete, and the size range is wide (three produce line can manufacture all non-standard sizes). The Minimum Order Quantity (MOQ) as low as ONE piece, and the date of delivery is short with excellent cost performance.
3 The sales and service team is professional and localize.
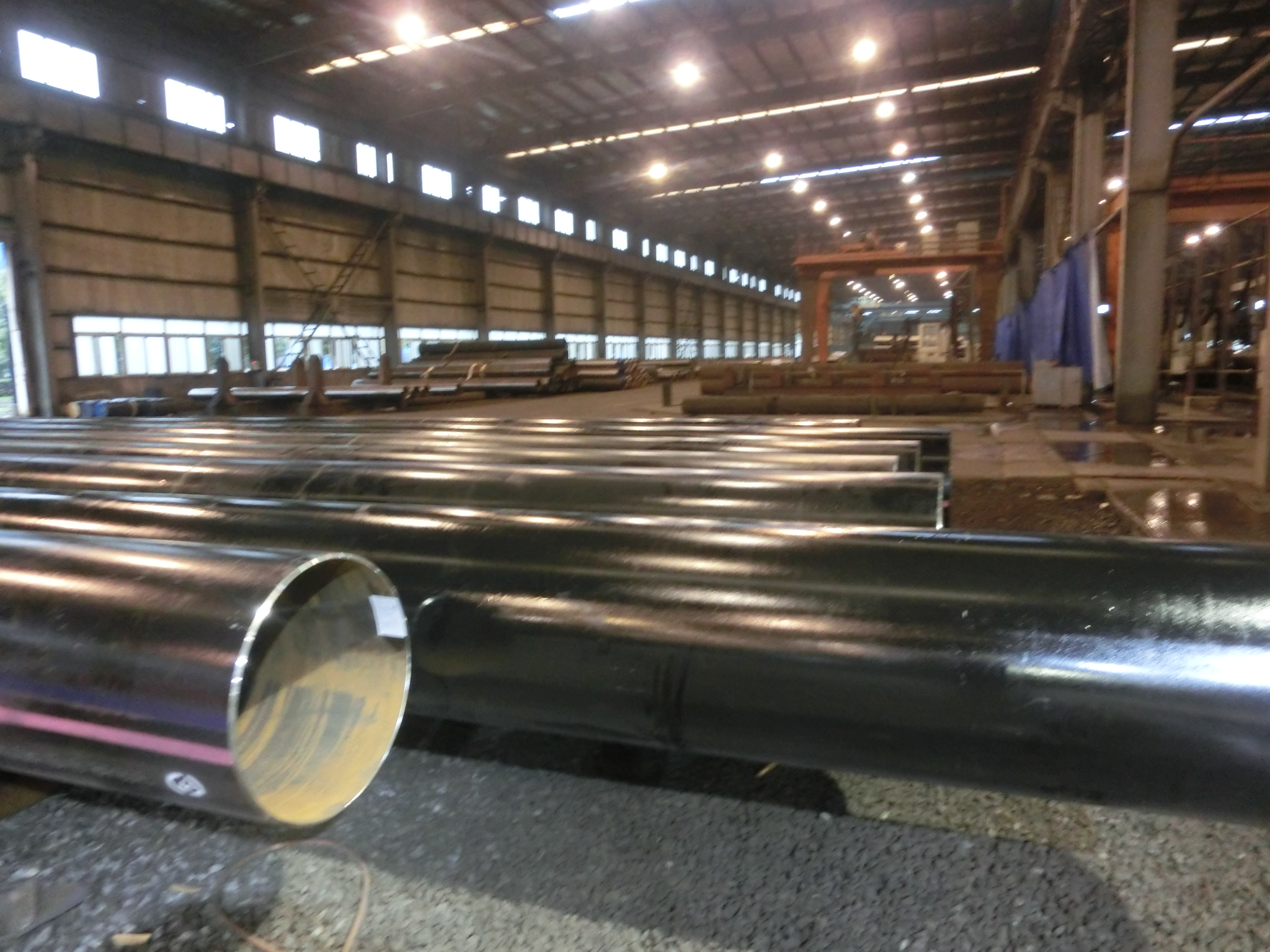
A106 Pipe,Asme Sa106 Carbon Steel Tube,Asme Sa106 Pipe,106C Pipe
YANGZHOU CHENGDE STEEL PIPE CO.,LTD , http://www.chengdepipe.com