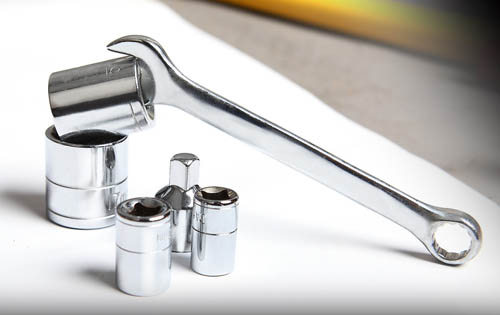
The global tool industry has undergone a remarkable transformation as it navigates through the challenges of the world's first planned economy era. Across all sectors, there has been a significant increase in production, with the tool industry standing out for its rapid expansion. By the late 1980s, leading enterprises and定点enterprises in the sector had established an annual capacity of 300 million high-speed steel cutters and over 10 million measuring tools. China became the top producer of high-speed steel cutters globally.
Meanwhile, our neighboring country Japan, a major player in tool manufacturing, reached a historical peak in high-speed steel cutting tool production with 120 million units annually. However, as the manufacturing industry evolved, the demand for standardized cutting tools declined, causing Japan's output to drop to around 90 million pieces.
Despite having a smaller manufacturing base compared to Japan, China managed to produce three times as many tools, entering a dangerously inflated production zone. This surge in quantity has significantly impacted the export market. Over the past five years, tool prices have plummeted multiple times, with some companies slashing prices by 40-50%. Domestic sales have barely reached $200 million, revealing the adverse effects of overproduction.
Compounding the issue, during the mid-to-late 1980s, buoyed by optimistic market forecasts, key players in China’s tooling sector not only expanded their operations but also fostered numerous joint ventures to boost production capacity. Many of these joint ventures eventually broke away from their parent companies to pursue independent growth. Additionally, some employees of state-owned enterprises ventured into private and township enterprises, forming the first wave of privately owned tool businesses in China.
These enterprises are more agile in their operations and free from the historical baggage of state-owned entities, potentially emerging as a driving force in the tool industry's reform and development. However, due to limitations in talent, technology, equipment, and management, many of these firms continue to prioritize quantity over quality. Within a decade, the total volume skyrocketed to billions of items, mostly concentrated in low-end products like twist drills, construction drills, woodworking tools, and calipers.
While the sheer volume is impressive, sales from these low-end products account for only about 30% of the domestic market’s total value. Due to branding and quality issues, these products have not penetrated formal manufacturing tool distribution systems domestically or internationally. Nonetheless, they have severely disrupted China’s tool export market.
Strategic missteps in the industry have led to a structural imbalance in the market. The second major error in the tool industry’s development strategy was its failure to adapt to technological advancements and globalization. The opportunity to upgrade China’s tool products and services was missed, widening the gap between China and foreign competitors.
Over the past two decades of reform and opening-up, China’s tool industry has failed to close the gap with foreign countries; instead, it has widened. This reality is hard to ignore.
In the 1960s and 1970s, Western developed nations transitioned into the "post-industrial development stage." Since the 1980s, they have progressively embraced information technology, biotechnology, renewable energy, and advanced materials—high-tech industries reshaping traditional sectors. The knowledge economy or new economy brought forth a wave of high-tech innovation transforming traditional industries.
Rapidly integrating information technology, automation, modern control, and management technologies has elevated mechanical products and services to unprecedented levels. This transformation imposed unprecedented demands on tool products, particularly in precision, efficiency, reliability, and specialization—often referred to as the "three high and one specialty."
This demand directly contradicted the traditional approach of standardizing, generalizing, and serializing product development. For example, the new four-roll twisting process, developed in the early 1960s, was quickly phased out in developed countries by the early 1980s.
Recognizing the need for modernization, the global tool industry shifted its focus toward achieving "three high and one specialty," abandoning outdated models for a new paradigm. Achieving this required substantial financial and intellectual investments. By the time China recognized the urgency, the window of opportunity had closed. Companies with weaker resources gradually lost momentum and withdrew from the market.
These developments explain why China’s stagnant tool industry now lags behind rapidly advancing foreign competitors—a natural consequence of missed opportunities.
Recently, industry insiders have lamented weak market demand and sluggish sales. In reality, the market demand structure is evolving, but the production structure remains unadjusted, creating a structural imbalance. Statistics from 1998-2000 show that imports of cutting tools rose from over $40 million annually to over $80 million. This indicates robust demand for high-tech products.
Survival in the market requires adaptation. Reflection: Without innovation, there is no way out. The tool industry must adopt new survival and development strategies in competitive markets.
Transitioning to a market economy, companies must first establish their correct position:
- Where are our strengths?
- Who is our target audience?
- How can we serve them?
Accurate positioning is essential for business development. The aim is to leverage strengths and outperform competitors. We must learn from the planned economy era, avoiding the trap of trying to be everything to everyone. Doing too much without focusing leads to inevitable failure in market competition.
Considering China’s current tool industry landscape, it’s clear that in traditional standardized tools, Chinese products remain competitive in both domestic and international markets. This edge should be preserved and built upon, but we must avoid盲目expansion or chaos.
In modern tools and specialized technical services, however, there remains a significant gap compared to international leaders. Yet, in the global tool industry, large multinational corporations are rare, while thousands of small and medium-sized enterprises thrive by specializing and excelling in niche markets.
As China’s tool industry moves toward modernization, it must chart its unique path, starting with small, specialized steps. Large and medium-sized tool companies should not overestimate their capabilities. During technological innovation and improving competitiveness, they must focus on key areas and avoid blind expansion.
This realistic positioning will unleash the full potential of the industry and accelerate modernization.